The first series Unimog was delivered 75 years ago.
Like a proverbial phoenix from the ashes, a miracle of technology emerged from destroyed post-war Germany in 1949. Not only is it a master of agriculture, it also captures the hearts of everyone for whom true performance means going to the limits of what is possible...and beyond. Three quarters of a century ago, a new era in automotive history dawned: with the delivery of the first series-produced Unimog.
Revolution according to plan.
Germany, spring 1949. On 19 March, in a small village called Hößlinswart, somewhere in the Rems-Murr district of Baden-Württemberg, in the south west of Germany, a customer was eagerly awaiting a very special delivery. From Fellbach, 20 km away, general distributor Kloz was transporting the first universal motorised unit to its proud new owner. The 70200 model series vehicle with chassis number 003 had been produced just a few months earlier by mechanical engineering company Gebrüder Boehringer in Göppingen, Swabia. Its promise: a revolution in agriculture.
The first Unimog was a technological masterpiece that stood out significantly from conventional tractors. This innovative spirit of German engineering also lives on in today’s Unimog, which is used worldwide in various sectors such as municipalities, the fire service, agriculture and disaster relief. The wildest dreams of its inventors have come true.
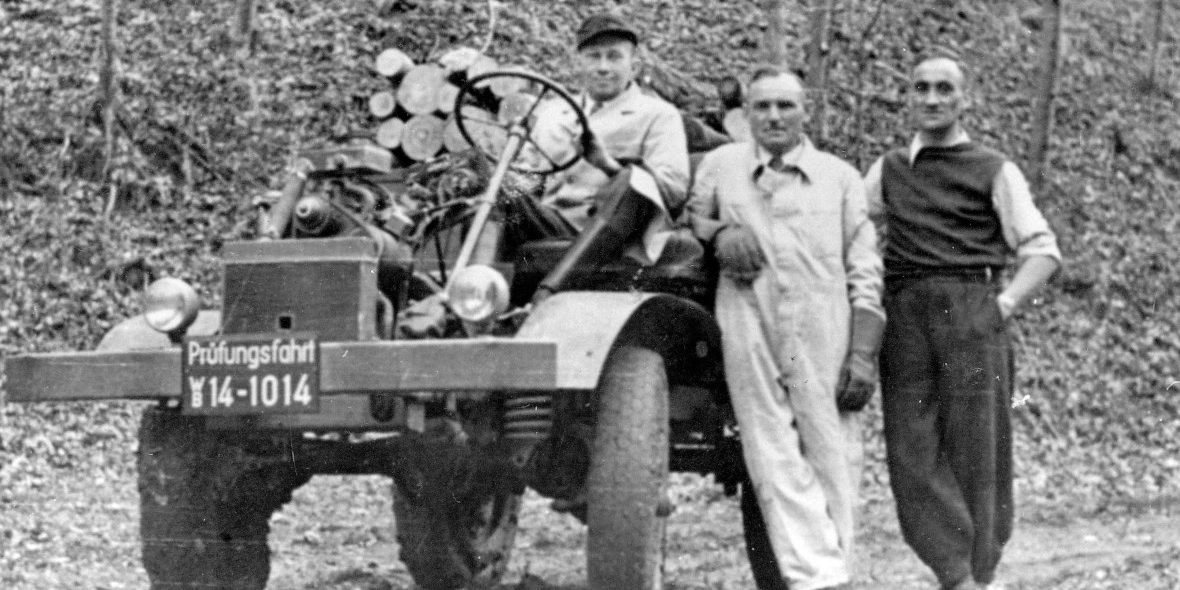
What makes the Unimog implement carrier
so special?
From brainwave to glimmer of hope.
The year is 1949, and the Germans are in the thick of rebuilding their communities. An economic miracle seems far away, and with tensions brewing between the East and West, dark times appear to be looming again. Yet in the midst of all this doom and gloom, a man in Schwäbisch Gmünd had a brainwave that became a glimmer of hope.
Albert Friedrich worked as a technical manager at gold and silverware factory Erhard & Söhne. But gold and silver had not always been his business: previously, Albert Friedrich, originally from Munich, had been in charge of the development of aircraft engines at Daimler-Benz.
In autumn 1945, the engineer decided to develop a multi-purpose agricultural machine to meet the enormous demand for agricultural tractors for small and medium-sized farms at the time. In November, he received the production order from the Allies. Albert Friedrich had been granted permission to manufacture ten test vehicles.
A character that has stood the test of time.
Friedrich’s plan was to come up with a versatile all-wheel drive machine generating 25 hp that could be used as a tractor, a stationary drive unit and a delivery vehicle.
This was to help facilitate agricultural reconstruction work during the post-war years. At the same time, it was important to comply with the strict requirements of the Morgenthau Plan that were in force at the time. Friedrich was able to win over his employer Erhard & Söhne as a partner for prototype production and Daimler-Benz for the supply of the engine with the designation OM 636. The vision he pursued was that of a compact vehicle similar to a two-axle tractor. On the face of things, that is. Because the truly revolutionary features were hidden under the bonnet.

Built to last forever.
Albert Friedrich’s design had four wheels with all-wheel drive and differential locks for the most difficult areas of use, as well as coil-sprung portal axles and drive shafts protected by torque tubes to safeguard ground clearance. The track width of the vehicle was 1,270 mm, which, at the time, was the same as exactly two rows of potatoes.
Albert Friedrich also designed a folding top and a folding windscreen for the special vehicle, as well as fixtures for driving agricultural implements at the front, a towing device at the rear and a small loading area behind the cab. It would turn out that these characteristic building elements would last much longer than the German post-war years. Some may say that the vehicle is built to last forever.
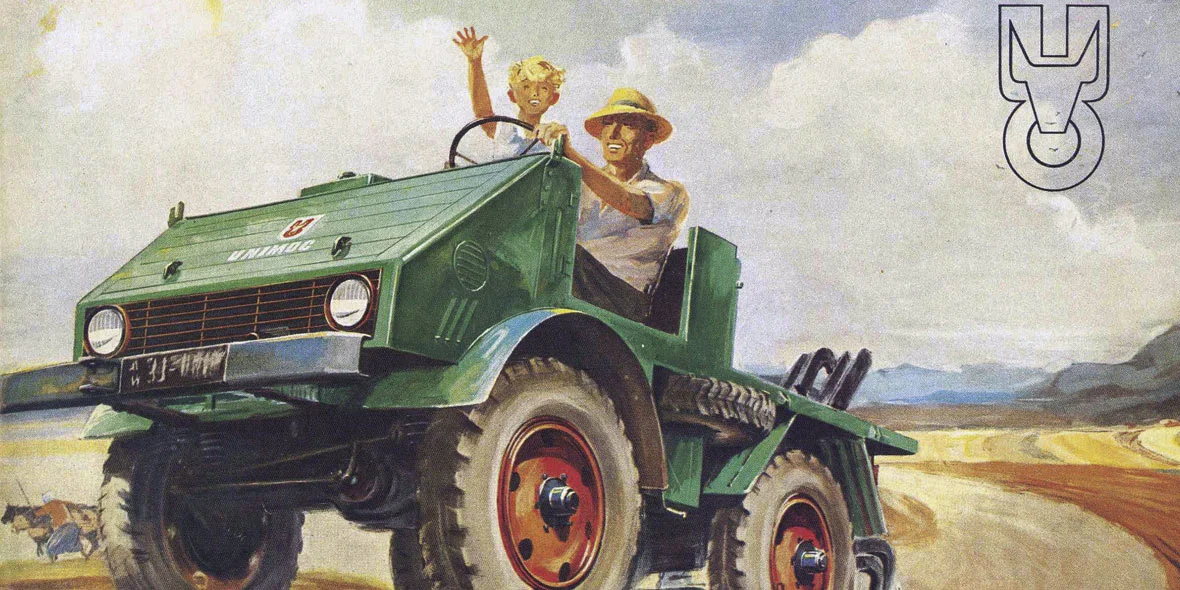
A snazzy name.
In order to help make his ambitious plan a reality, Albert Friedrich was able to win over leather goods manufacturer Franz Catta as a financial supporter and gather a team of talented engineers around him. One member of this team was Heinrich Rößler, who had previously worked in passenger car and engine development at Daimler-Benz and had gained experience as an assistant in agriculture after the end of the war. He was appointed senior designer.
Starting in 1946, Heinrich Rößler and his team developed the first prototypes on Erhard & Söhne company premises. The first test drive with the U 1 took place on 9 October. Hans Zabel, another member of the engineering team, gave the new vehicle the snazzy name “Unimog”. The abbreviation stands for “Universal-Motor-Gerät für die Landwirtschaft” (universal motorised unit for agriculture) and is intended to underline the versatility of the vehicle as well as its perfect suitability for the agricultural industry.
Around two years later, on 29 August 1948, the Unimog was presented to the public for the first time at the German Agricultural Society (DLG) exhibition in Frankfurt am Main. The response was overwhelming: the new vehicle immediately found 150 interested customers.
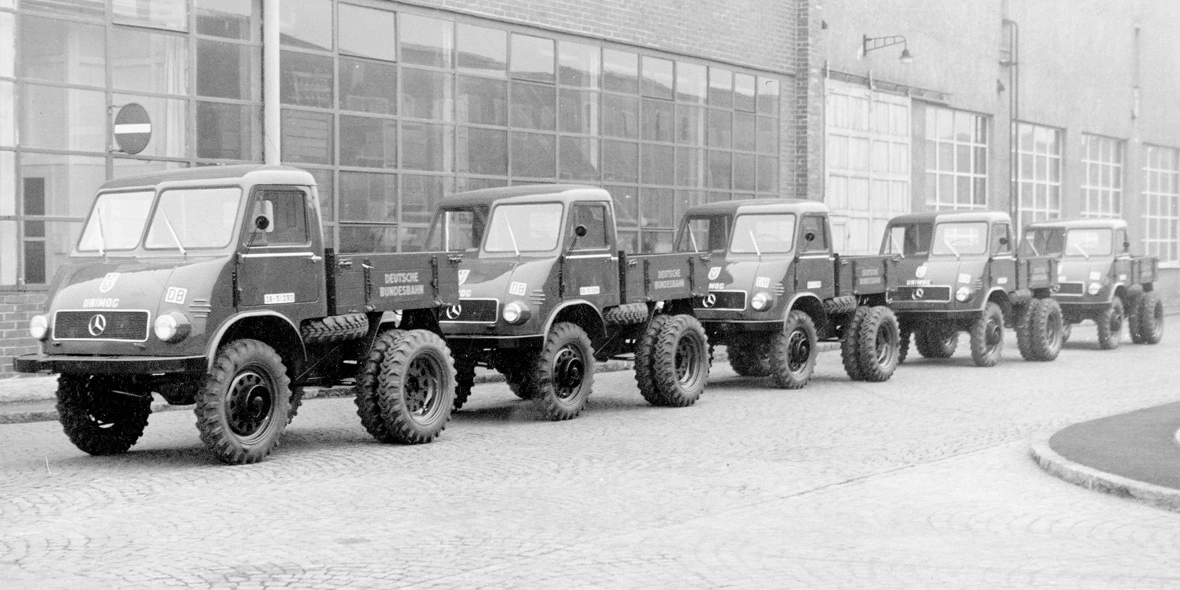
Into the next dimension with Daimler.
Rolf Boehringer, machine manufacturer at Erhard & Söhne, then took over the industrial production of the universal motorised unit. In 1949, Gebrüder Boehringer began series production in Göppingen. Up to 50 Unimogs, a total of 600 units of the Unimog U 70200 model series, were produced each month – without a production line and largely by hand. At the same time, the Unimog also tapped into new application areas: 44 of the 600 units went to the Swiss Army.
Some of the first models are on show today in the Unimog Museum in Gaggenau: the prototype U 6, the second oldest remaining Unimog and a Unimog from the first series with model designation 70200.
In 1950, Unimog fathers Albert Friedrich and Heinrich Rößler handed over the Unimog business and development team to manufacturer Daimler-Benz, which, from then on, took over large-scale production. Today, the price paid for the handover seems quite incredible: 600,000 German Marks. In comparison: in 1962, worldwide sales of the U 411 amounted to as much as 54,870,000 German Mark, excluding the spare parts business.
Production launched in Gaggenau in 1951, where significant improvements were soon introduced with the 401 and 402 model series – particularly the closed, shock-resistant and impact-resistant all-steel cab.
From 1953, the Unimog was equipped with the Mercedes star. This is a quality feature that was set to inspire engineers to continuously evolve the Unimog. From mid-2002, the Unimog has been manufactured at the new production site in Wörth.
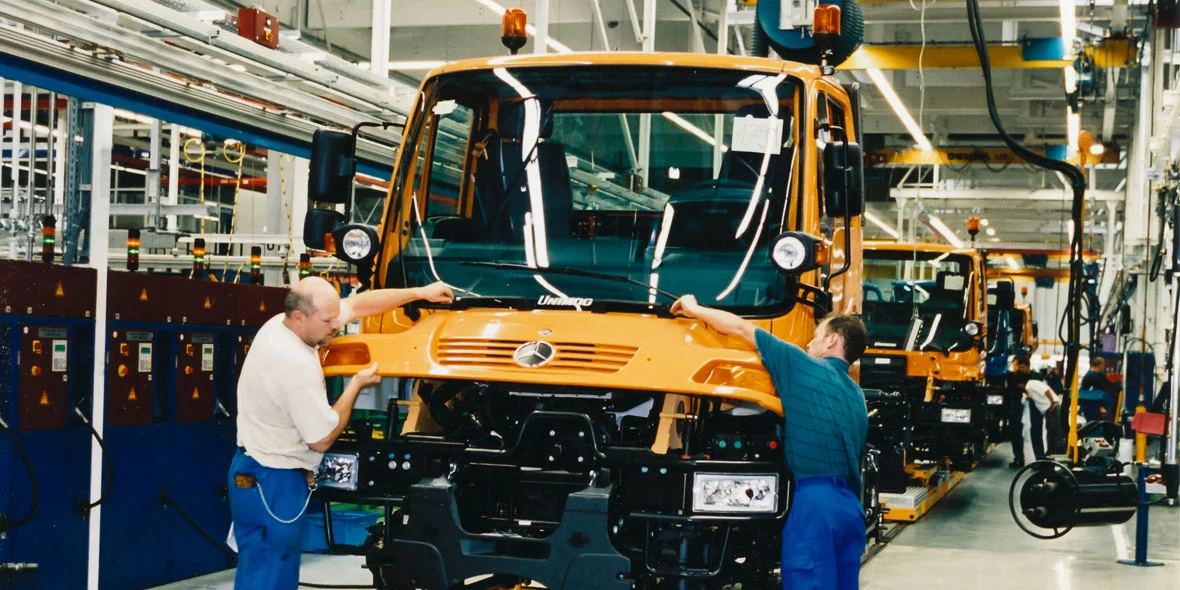
Constant, but also: innovative.
A lot has happened since that first Unimog delivery back in 1949. Since then, more than 375,000 Unimogs have rolled off the production line. For seven decades, the vehicle that was built to revolutionise agriculture has proven itself as a work horse in numerous versions as the Unimog U 219 to U 535: in municipal operations, the fire service, the construction industry, two-way operation or agriculture and forestry. With around 1,000 different applications, the Unimog implement carrier is still at the forefront of what is technically possible.
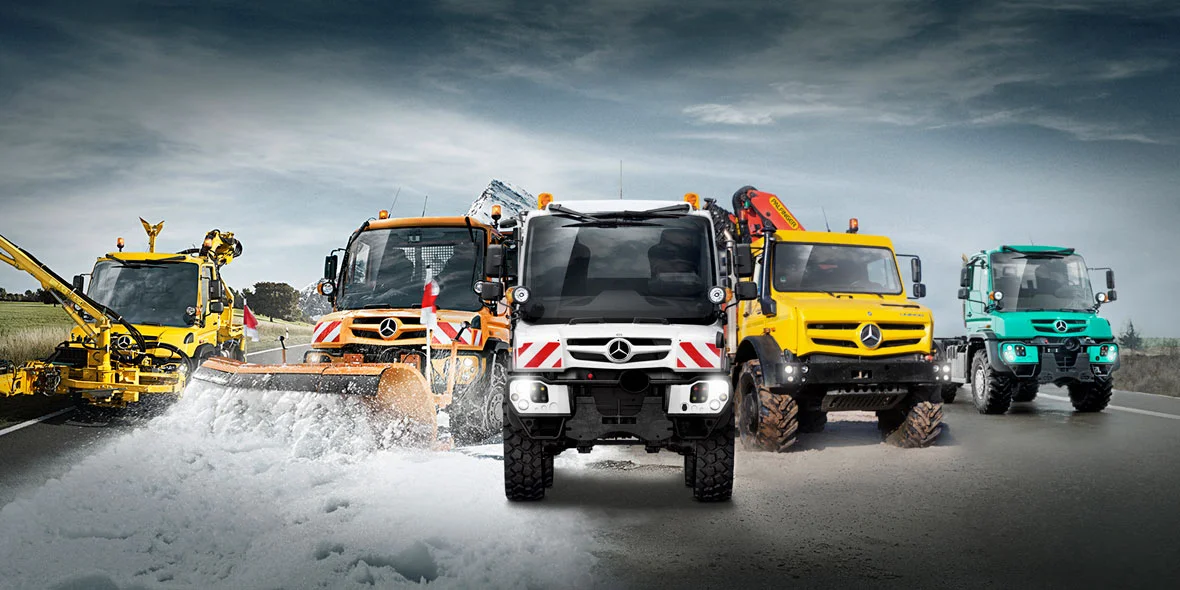
The Unimog has always remained true to its DNA, the basic concept of its inventor Albert Friedrich, with all-wheel drive, portal axles, coil springs, and attachment and body options at the front and rear. And yet this marvel of technology is constantly reinventing itself:
to name just one example, the highly off-road-capable Unimog model series U 4023 and U 5023 boast extreme off-road capability and extremely torsionally flexible axles – so they can bring builders, fire service crews and emergency services to places other vehicles fail to reach.
Want to find out more about
the extreme off-road Unimog?
Unimog: more than just the past.
In addition to technical optimisations such as hydrostatic drive and hydraulic spring, with which the Unimog's frame can be lowered and stabilised, Daimler Truck is also actively working on new revolutions. These include sustainable drive technologies to achieve the goal of climate neutrality by 2039.
Part of the development strategy for the transformation to carbon neutral transport is, for example, the "WaVe" (German acronym for hydrogen combustion engine) project, in which Daimler Truck is actively exploring the possibility of drastically reducing CO2 emissions by using hydrogen as a fuel. All this in addition to the Group-wide conversion to battery operation.
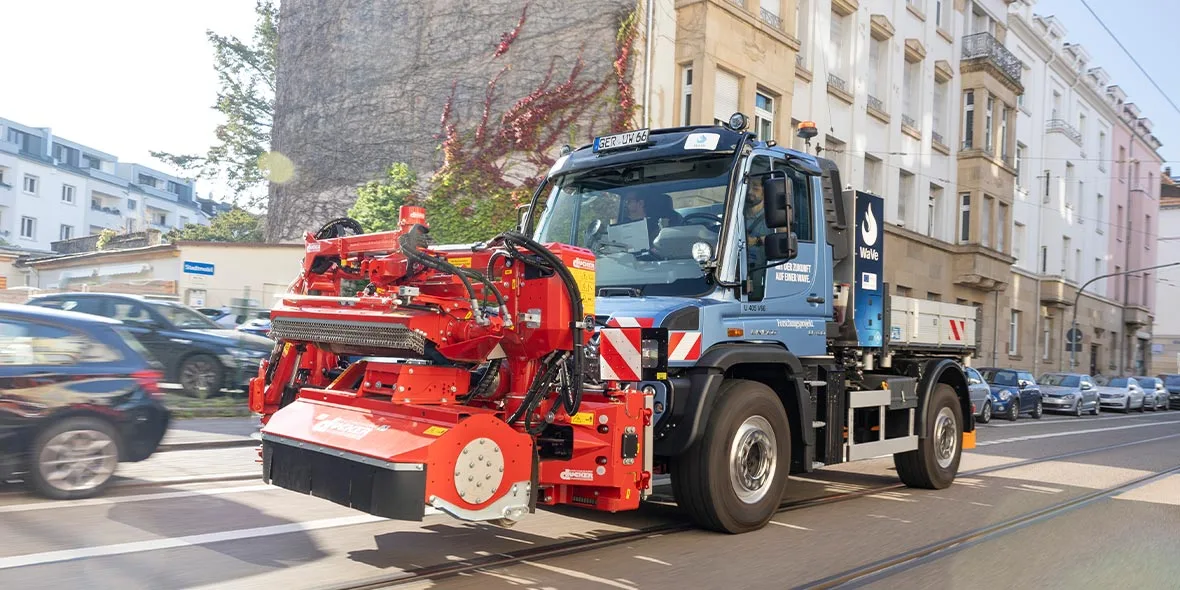
Future in series production.
In 2024, Daimler Truck will continue to prove that even the oldest of vehicles are able to reinvent themselves... over and over again.
In May, the implement carriers will be equipped ex works with the new UNI-TOUCH® operating system, which allows the person behind the wheel to adapt selected work processes to their individual demands in a highly convenient way.
The UNI-TOUCH® operating system is simply superb. And superbly simple.
In July 2024, the Unimog will take another step towards the future. The safety assistance systems provided as part of the EU General Safety Regulation (GSR) fine-tune Daimler Truck's safety concept. These clever, digital traffic assistants can protect road users even better from dangers and at the same time help to relieve the burden on the driver.
This is the Unimog with GSR features.
75 years after the first series-production Unimog was delivered to that small village near Stuttgart, the Mercedes-Benz all-rounder goes into series production once again with state-of-the-art technology.
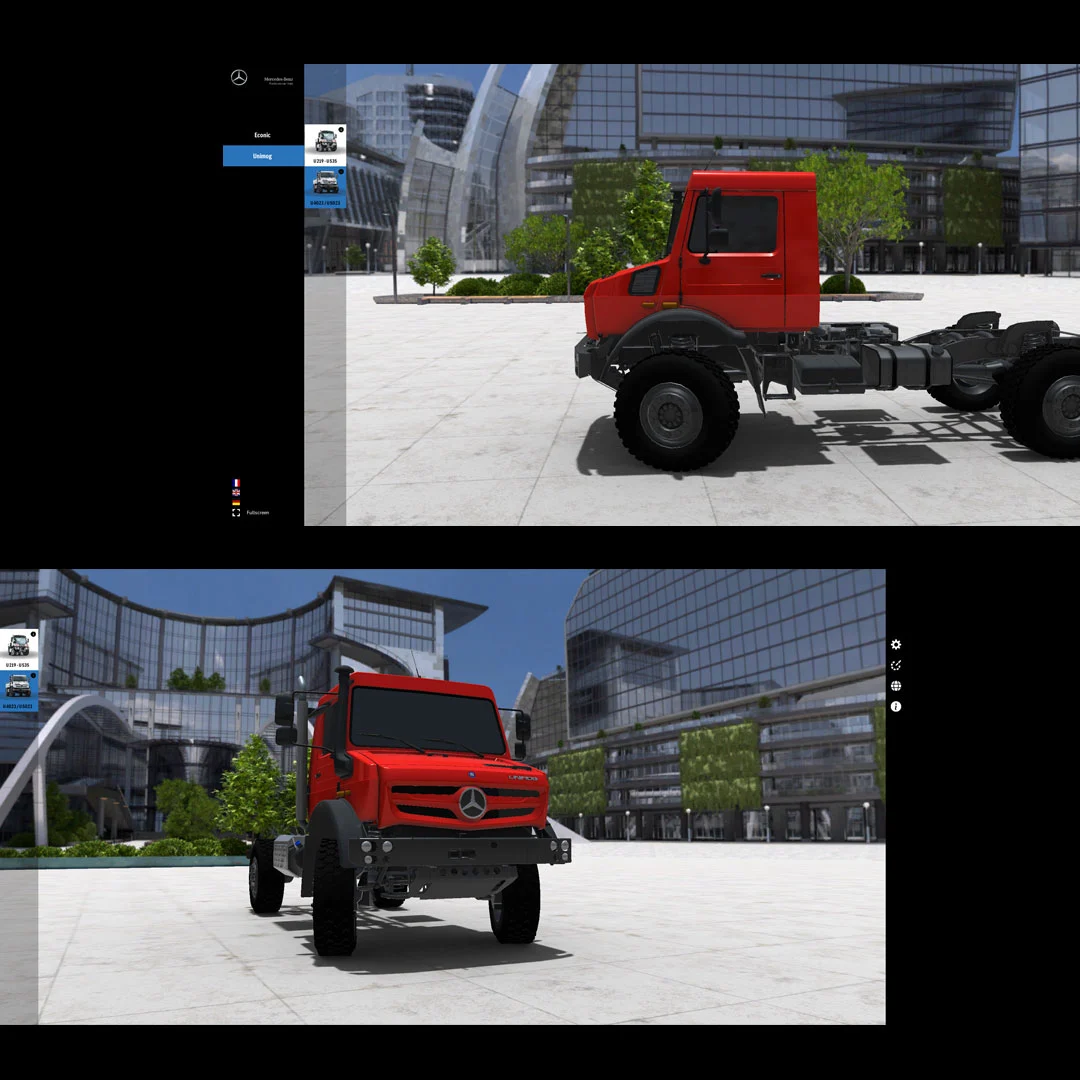
Have you tried it out yet?
Choose from a wide range of selection options
to create your personal favourite in the Unimog 3D product designer.