The Unimog bravely defies the adverse conditions of open pit mining.
A journey into the Hambach open-cast mine is truly impressive. A lunar landscape of gigantic proportions - dominated by eight bucket wheel excavators that are among the largest of their kind in the world. Sascha Funk has been working for RWE Power AG for 10 years and, together with his colleague Jörg Rübsteck, is responsible for procuring material and vehicles for the gigantic fleet.
“Our total fleet comprises around 800 vehicles, from electric cars for business trips and courier deliveries between the locations, to 40-tonne trucks for transporting materials in the pit,” says Sascha Funk, describing the extent of his work duties. Jörg Rübsteck is primarily occupied with procuring Unimog vehicles for the RWE fleet: “I have been handling Unimog, specially tailored to our needs, for 15 years. They have been an integral part of our vehicle fleet for over 40 years, and we have enjoyed highly constructive cooperation for all that time,” he reports. RWE's reliable partner is the Unimog general agency RKF-Bleses GmbH, from advice to service.
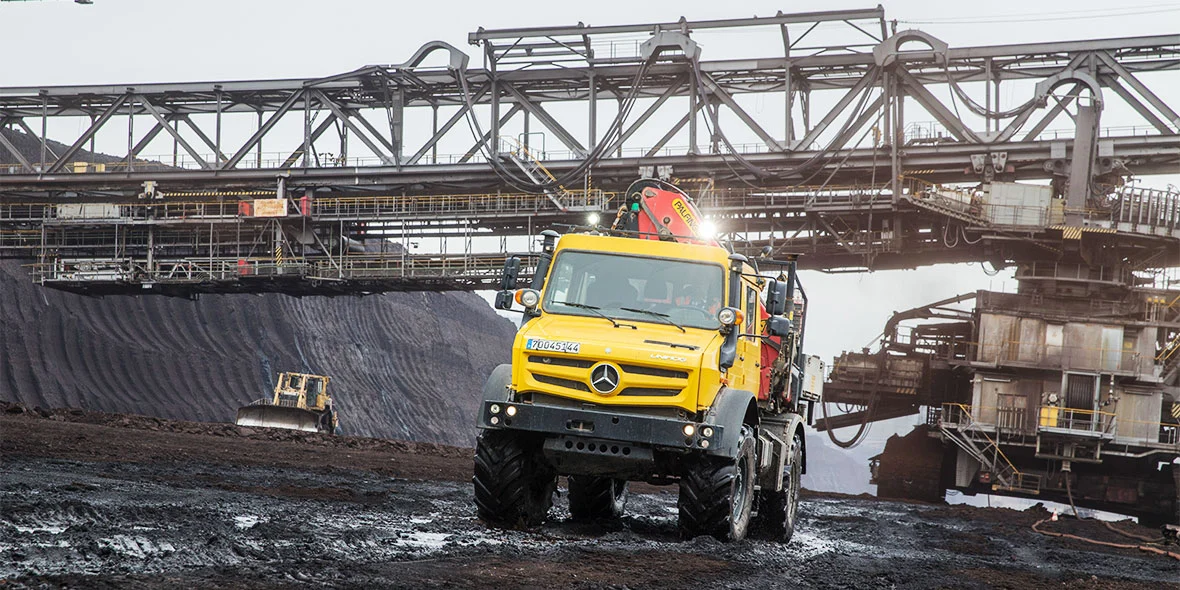
126 Unimog ensure trouble-free operations.
The Hambach open-cast mine has long been regarded as the ideal test site - including for the 126 Unimog vehicles in the fleet. “Most of our Unimog vehicles are equipped with a flat bed, a crane and a winch. They are the tools we need most,” Jörg Rübsteck explains. A U 5023 with a built-on crane has just been put into service; shortly before that, a U 4023 with a flat bed and a large double cab.
The special challenge is the difficult ground - a highly unusual mixture of sand, lime, clay, rock and water, which continually penetrates into all the vehicle components and causes heavy wear. “We’ve even had vehicles with their brakes completely worn down after just one hard day,” Sascha Funk says, highlighting the extreme conditions on-site. That is why all the Unimog units at the Hambach open-cast mine have an encapsulated final reduction gear. As well as dealing with the unusual ground mix, the vehicles are essentially run continuously in heavy mud. That is because the pit is permanently watered in order to prevent huge plumes of dust.