Unimog U 530 and U 430 units make sure the power grid stays online.
For its maintenance work, operator ED Netze employs Unimog to lift overhead cable engineers up to their working height, remove rotten poles, dig deep holes, and install new composite poles.
In dizzy height with the Palfinger crane.
The hydraulics just have to raise the last section of the Palfinger crane a few more centimetres, then operator Michael Leiber up in the cage can get started. The 20 KV cable has long since been disconnected and grounded. The engineer quickly releases the fixings, then he detaches the power conductors from the insulators. Today the pole is scheduled for replacement. It has to make way for a so-called "wood replacement pole". The inspector has marked it with the standard red nail, indicating that it is rotten.
"It's not actually that old. But since chemical additives are taboo nowadays, the fungal infestation has gradually got worse. And it's no longer as weather-proof as it was," explains Dirk Umland, coordinator of the nine-man crew of overhead cable engineers employed by ED Netze to cover the southern Baden region. The poles are normally replaced after 10 years. Then it's Thomas Quast's turn to go to work – with a chainsaw. It cuts through the aged wood in no time. The long end of the rotten pole dangles only briefly on the crane, which places it gently down among the tall grass together with the porcelain insulators. "The insulators are not thrown away; they are re-used after being inspected."
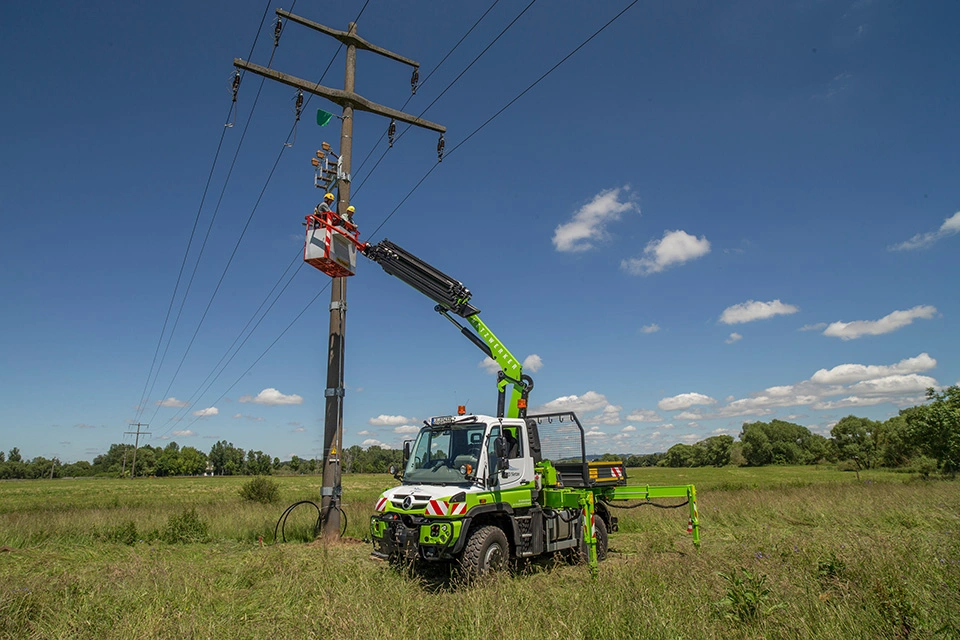
Unimog U 530 equipped with a two-bucket grab.
After the wooden stump has been levered out of the ground, excavator operator Thomas Quast digs the new post-hole. To do the job, the green U 530 – which, like the slightly shorter U 430, was added to the operator's vehicle fleet in late 2015 – has been retrofitted with an Ematec excavator unit. The two-bucket grab quickly makes the hole deeper, aligning itself perfectly thanks to its rotary motor.
The engineer excavates the soil with great precision – though his colleagues continually measure to check that the necessary depth has been reached. A sixth of the length of the pole is the rule. Finally it's ready: the new, 225 kilogram pole is carefully hoisted up using the hydraulic crane. The operator with the four-way radio remote control pushes the steel pole with its glass fibre-reinforced plastic top into the desired position with the greatest possible precision using the crane's hook. The new pole is a two-part construction, the bottom section made of steel, with a cylindrical glass fibre-reinforced plastic tube on the top. The design serves as a bird guard, as well as for connecting cross-beams.
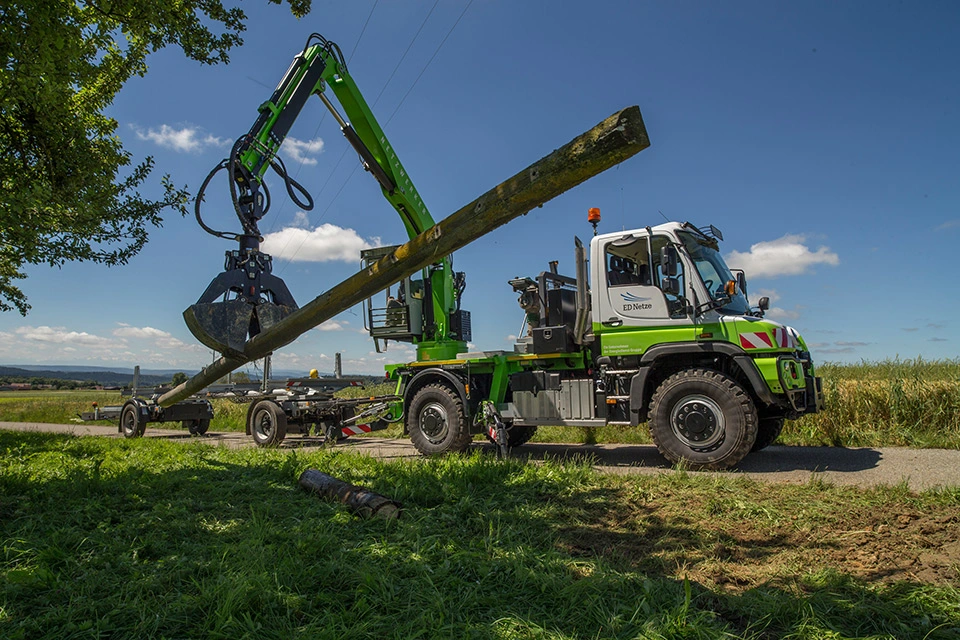
Despite the high-tech equipment, the measurements are taken by analogue means.
Now measurements are taken – by old-fashioned analogue means. Thomas Quast checks the installation position repeatedly with a plumb line. Colleague Siegfried Müller has to adjust the crane – always kept stable by its four supports – a little more until Quast is finally satisfied. Then it comes down to shovelling earth into the hole, after which newcomer Benedikt Baumann can demonstrate that he's learnt how to use the hand-operated pneumatic compressor. The layer of earth around the new pole gradually grows. The compressor jigs for half an hour, then the new pole is solid as rock. Siegfried Müller retracts the Palfinger crane's six telescopic arms. The cage then has to be run out to the end of the crane again, to fix the cables.
Workload of about 800 poles a year.
The maintenance crew checks some 800 poles a year, wrapping them in foam and a film covered with impregnating salt as necessary. "That isolates the pole from the soil," Müller explains. His team also routinely inspect cables and poles. The four-man team normally replaces two poles a day. Around 250 are replaced each year across the network.