A Unimog U 318 in service for the van Meeteren forestry administration.
Pulling trees, splitting wood, filling feed cribs, loading bales – for a year now, the Udo van Meeteren forestry administration in the Eifel village of Wallersheim has been using a Unimog U 318 and demanding everything from it. It is used to maintain an area of 760 hectares of meadows and mixed forest, which also includes an abundant red deer population. How does the new implement carrier perform on day-to-day duties in the forest?
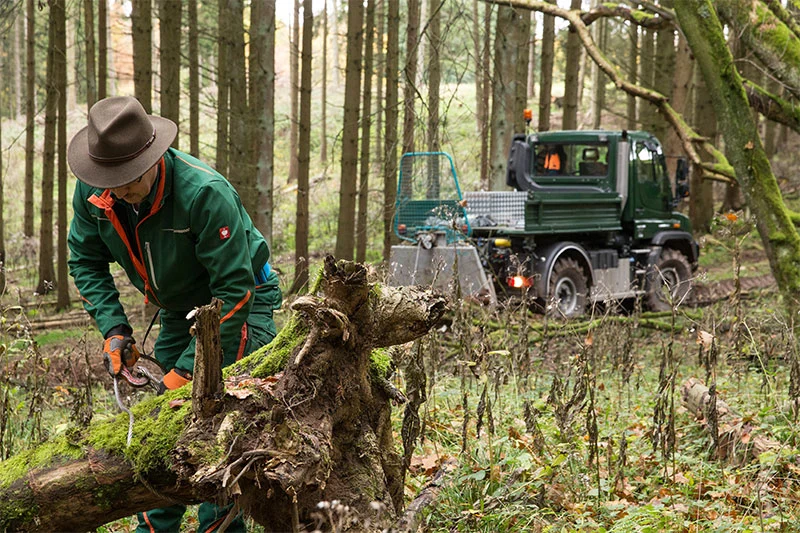
There's a click.
There's a click as the hook snaps shut. Karl-Heinz Dringen casts a final glance at the steel loops he has laid over the impressive log before he presses on the remote control. Suddenly, the steel cable gets taut and the hydraulically-driven winch at the rear of the fir green Unimog sets into motion across the clearing. The tree trunk is drawn up to just a few metres distance from the vehicle and then the forester gets behind the wheel. Four deep-treaded Michelin XM47 tyres set the 177-hp-strong powerhorse in motion. The trunk is freed and then released in readiness for the chainsaw which is always close at hand in the self-built light-alloy stowage box on the platform of the U 318.
Even in logging operations, the new BlueTec 6 Unimog variant proves that it can handle multitasking with ease whilst also tackling more tasks than your average towing vehicle: the winch is put back in place in the machine storage hall using the rear power lift and swapped for the hydraulic wood splitter. A hydraulic upper control link forms the upper connection between the rear of the vehicle and the auxiliary lift unit, and only the Söder 80-kW power take-off shaft – available as optional equipment for the "agricultural vehicle rear" – has to be connected up with the shaft connection of the splitter's drive unit. The required 540 rpm for the rear power take-off shaft need the 5.1-litre engine to turn at an engine speed of just 1550 rpm, for example, and thus the stationary throttle level only needs to be increased slightly. Then the wood splitting can start. The entire stock of oven-ready firewood will then be loaded into the trailer a short time later. "Without the Hauer front loader, that would take quite a lot of time", explains Dringen, whilst hooking up the drawbar of the Scharmüller trailer coupling to the Unimog with a single movement. "The Ringfeder coupling on the old U 300 was often a bit of a faff. If it wasn't perfectly aligned, it would cause problems when coupling up."
Economical change: from MB trac to Unimog.
Until 2006, Karl-Heinz Dringen had spent five years carrying out all of his forestry transport, mowing, sowing, planting, clearing and pathmaking tasks with an MB trac 900 turbo. Then the forestry association opted for their first Unimog. A truly new era at van Meeteren – but an economical one: the first U 300 implement carrier with 4.2-litre displacement was even more economical thanks to its average consumption of 7.5 litres of diesel per operating hour. The U 300 already featured fully-proportional working hydraulics in which both hydraulic circuits offer flow rates of 25/50 litres/min with a maximum pressure of 200 bar. But in hindsight, there were some elements of the Unimog generation produced from 2000 onwards which were in need of some tweaking to suit forestry applications.
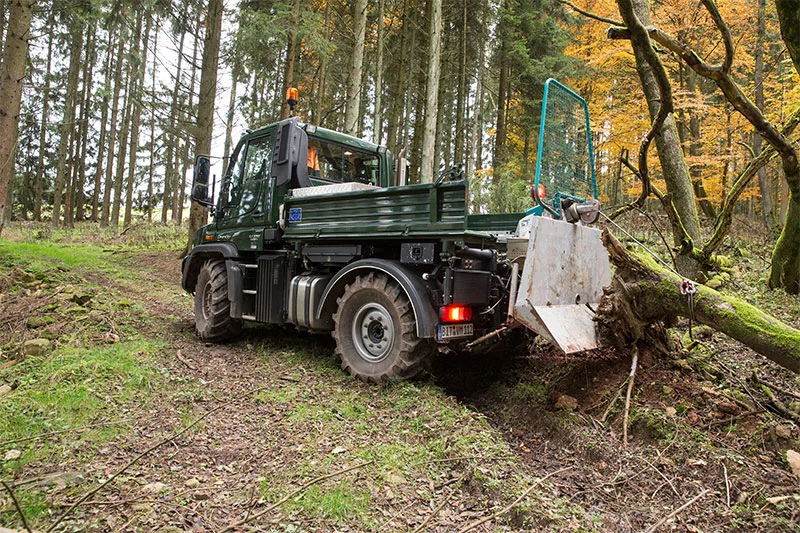
Comfortable and optimised: now a reliable all-rounder.
On the new U 318, the implement manufacturer of the front loader has better adjusted it to suit the chassis and can thus guarantee the required ground clearance. The man behind the wheel of the U 318 has also quickly come to love the now 300 mm higher implement pivot point (3620 mm instead of 3310 mm on the U 300) when stacking up the pallet cages in his machine storage hall. "Now loading the third level of shelves is easily possible," he confirms.
The forester has quickly got used to the hydrostatic drive which, in the new Unimog generation, offers the impressive possibility of rapidly switching between the manual transmission and back while driving, as well as providing steplessly adjustable propulsion at speeds of up to 50 km/h. Tasks involving the front loader are much more fluid thanks to this drive system as opposed to the previously required gear reduction. Karl-Heinz Dringen finds the new, ergonomic combined joystick with its two hydraulic positioning movements a massive help, allowing such commands as "raise" and "tip" to be carried out simultaneously when using the bucket loader.