Salzförderung unter Tage im Kalibergwerk Werra.
K+S fördert und veredelt seit über 125 Jahren mineralische Rohstoffe. Mit dem Econic sichert das traditionsreiche Unternehmen abgebaute Grubenfelder im osthessischen Kalibergbau.
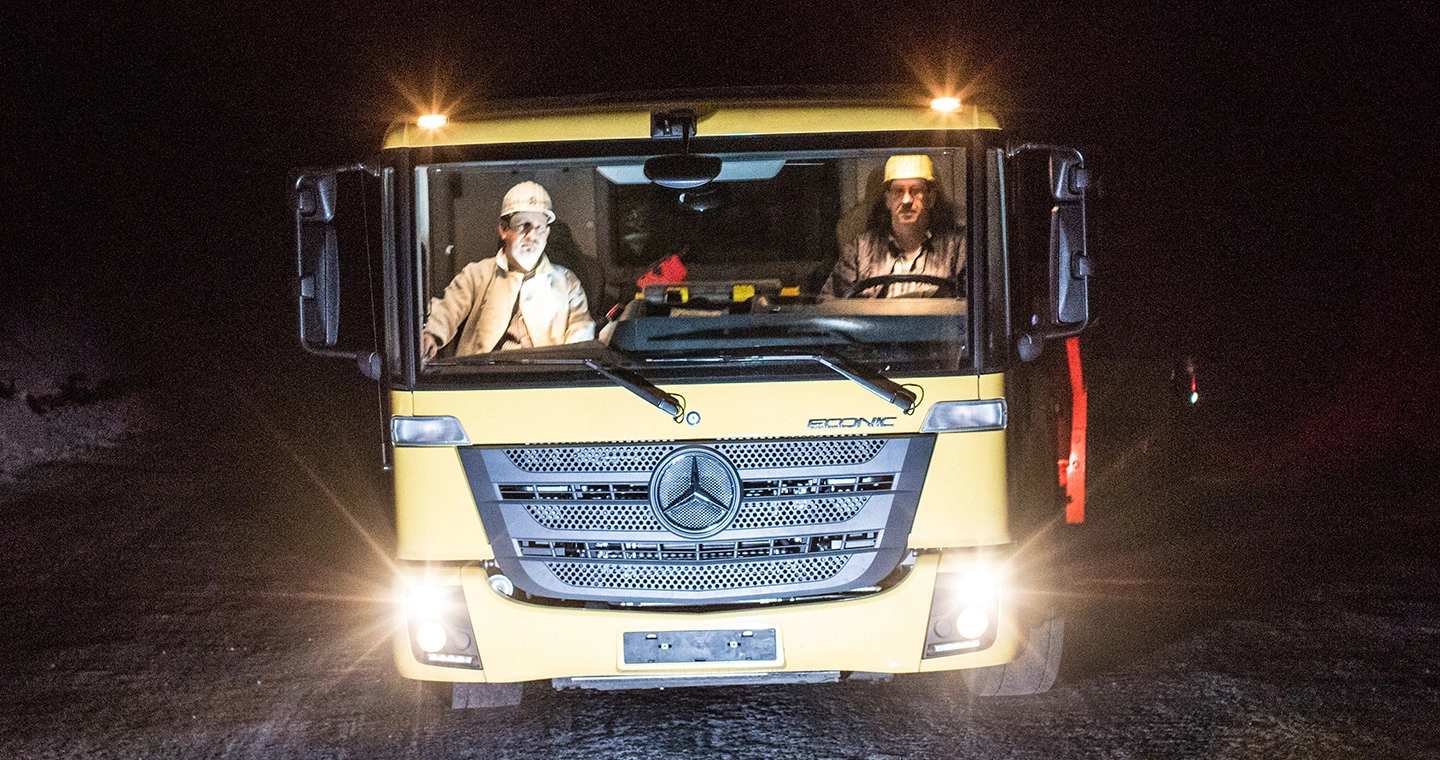
Rund 20 Millionen Tonnen Rohsalz werden jährlich zu Tage gefördert.
Der Schacht ist eng, der Weg hinab unter Tage düster und beklemmend. Mit mehr als acht Metern pro Sekunde schießt der knapp zweieinhalb mal drei Meter große Metallkorb zur Personenbeförderung in die Tiefe, vorbei an Millionen Jahren Erdgeschichte. Nach rund anderthalb Minuten erreicht die Seilfahrt ihr Ziel: die erste Sohle des K+S Kalibergwerks Werra – 750 Meter unter der Erdoberfläche.
„Alles, was wir hier unten brauchen, fährt durch solch einen engen Schacht ein“, erklärt Arnd Schneider. „Auch der Econic ist auf diesem Weg ins Bergwerk gekommen.“ Der 47-Jährige ist seit 2013 Betriebsleiter der Untertageverwertung bei K+S am Standort Hattorf. Die Anlage befindet sich rund 50 Kilometer nördlich der Barockstadt Fulda und gehört zum Verbundwerk Werra. Das riesige Kalibergwerk mit seinen Produktionsstandorten Hattorf und Wintershall in Hessen sowie Unterbreizbach in Thüringen fördert jährlich rund 20 Millionen Tonnen Rohsalz an die Oberfläche. Neben Düngemitteln stellt das Verbundwerk technische Salze sowie hochreine Produkte für die Pharma-, Lebensmittel- und Futtermittelindustrie her. K+S ist der größte Salzproduzent der Welt und gehört zur Spitzengruppe der internationalen Kalianbieter.
Das Salz lagert in zwei Sohlen in bis zu 1.000 Meter Tiefe.
„Die Kalilagerstätten hier im Werratal entstanden vor mehr als 200 Millionen Jahren durch Verdunstung des urzeitlichen Zechsteinmeeres“, sagt Arnd Schneider. „Relativ flache Kalilager, sogenannte Flöze, mit einer Mächtigkeit von nur zweieinhalb bis vier Metern enthalten das Rohsalz, das wir hier abbauen.“ Sie befinden sich auf zwei Sohlen in bis zu 1.000 Meter Tiefe. Seit mehr als 100 Jahren werden Kalisalze in Osthessen abgebaut, heute mit speziellen Großgeräten und moderner Technik. Im Lauf der Zeit ist ein Grubenkomplex von gigantischen Ausmaßen entstanden. „Das Werk Werra umfasst in etwa die Fläche Münchens und seiner Vororte“, sagt Bergbauingenieur Arnd Schneider, der sein Studium an der Technischen Universität Freiberg abgeschlossen hat.
Das gesamte K+S-Werk Werra beschäftigt annähernd 4.400 Mitarbeiter, davon rund 2.000 Bergleute. Knapp über 50 sind in der sogenannten Untertageverwertung eingesetzt, dem Verantwortungsbereich von Arnd Schneider. Ihr Ziel: die Sicherung älterer, bereits abgebauter Grubenfelder. „In begrenzten Bereichen des Bergwerks lagern wir mineralische Abfälle als Versatzmaterial ein. Das hat zwei Vorteile: Erstens werden sie durch die Einlagerung stabilisiert und zweitens nutzen wir die stofflichen Eigenschaften von Abfallprodukten aus der Industrie“, so Betriebsleiter Schneider. Das Versatzmaterial, größtenteils feinste Filterstäube aus Hochtemperaturverbrennungsanlagen, wird in Silo-Lkw oder in Big-Bags am Standort Hattorf angeliefert. Eine spezielle Konditionierungsanlage bereitet die mittels Druckluft förderfähigen Abfälle für den Versatz vor. In neue Big-Bags abgefüllt härtet die Mischung innerhalb kürzester Zeit aus. Die bis zu 1,2 Tonnen schweren Säcke gelangen dann über den Schacht ins Bergwerk.
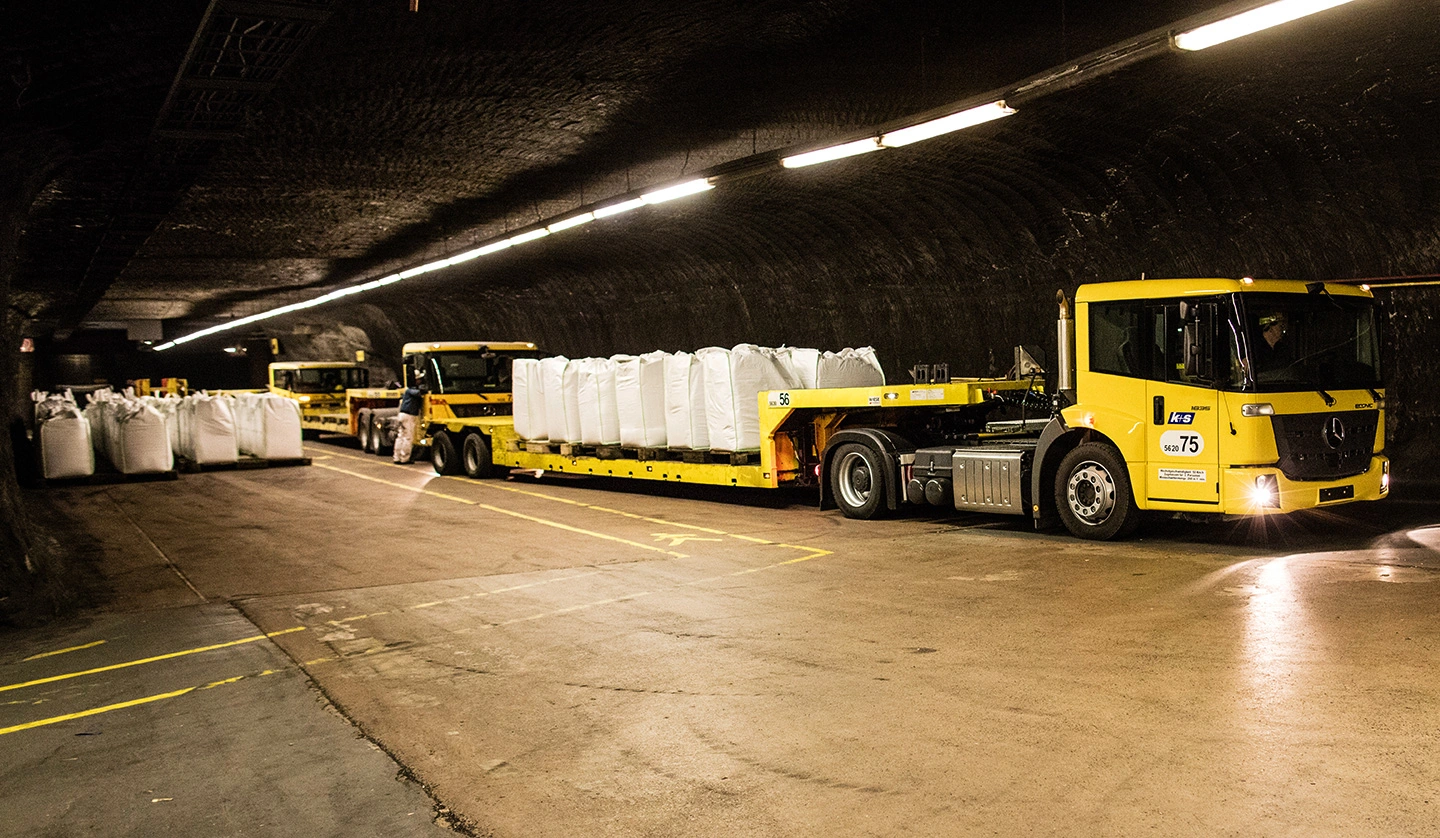
Kraftvoll und komfortabel.
Mehr als 1,5 Millionen Tonnen Versatzmaterial wurden dort bereits eingebaut. „Hier unten am Schacht nehmen wir die Big-Bags in Empfang“, sagt Mario Christ. „Mit dem Gabelstapler laden wir bis zu 16 Stück auf den Tieflader meines Econic. Dann fahre ich sie ins Versatzrevier.“ Der 48-Jährige steht seit 1992 im Dienst von K+S. Seit der Inbetriebnahme der Untertageverwertung 1994 ist der Bergmann bereits Teil des Teams. In drei Schichten, rund um die Uhr, sechs Tage pro Woche lagern er und seine Kollegen mittels Teleskopstaplern und dem Econic die Big-Bags in die alten Kammern des Kalibergbaus ein: Reihe für Reihe. Zwischenräume werden mithilfe einer umgebauten Schneefräse und Feinsalz aufgefüllt.
Arnd Schneider erklärt die Schwierigkeiten beim Unter-Tage-Abbau: „Unsere Herausforderung: Wir müssen mit knapp 20 Tonnen Ladung Steigungen von bis zu 14 Prozent überwinden. Das geht nur mit einem kleinen Kraftpaket wie dem Econic 1835.“ Der durchzugstarke Euro-VI-Motor OM 936 bietet mit 260 kW genügend Leistungsreserven – auch für steile Anstiege. Er ist serienmäßig mit einer Vollluftfederung ausgestattet. Die Niveauregelung des Zweiachsers lässt sich individuell einstellen, um beispielsweise die Bodenfreiheit den oft widrigen Straßenverhältnissen auf den Salzpisten im Bergwerk anzupassen.
Wir haben unter Tage nur eine durchschnittliche Deckenhöhe von weniger als drei Metern. Normale Trucks passen hier einfach nicht rein.
Arnd Schneider, Betriebsleiter Untertageverwertung Standort Hattorf
Funktion
Hohe Zugkraft, kombiniert mit kompakten Außenmaßen und niedriger Fahrzeughöhe – der Econic-Sattelzug zieht schwere Lasten durch die steilen und engen Korridore des Kalibergwerks.
Ausstattung
Der Reihensechszylinder OM 936 holt aus 7,7 Litern Hubraum 260 kW Leistung heraus.
Das sparsame Euro VI-Aggregat bietet somit genügend Leistungsreserven für anspruchsvolle Aufgaben – auch tief unter der Erdoberfläche.
Effekt
In den Kaliflözen des K+S-Werks Werra findet man Anstiege von bis zu 14 Prozent. Der Econic 1835 kommt dabei nicht aus der Puste und befördert flink tonnenschweres Versatzmaterial zur Grubensicherung. Dank seiner Außenhöhe von nur 2 380 Millimetern ist er beinahe überall im Bergwerk einsetzbar.
Voll beladen schafft der Econic Tempo 50.
Der Econic mit einer 2.380 Millimetern Außenhöhe kann zudem – wenn es an der Grubendecke doch mal eng wird – bis zu 50 Millimeter abgesenkt werden. Für die Arbeit in der Tiefe wurden die beiden neuesten der insgesamt 13 Econic, die in der Untertageverwertung von K+S eingesetzt werden, nur geringfügig modifiziert. „Wir haben eine Heckscheibe eingebaut, ein Kühlaggregat auf der Fahrerseite musste einige Zentimeter höher gelegt werden, und die Abgasanlage ist nach oben hinter die Beifahrerseite gewandert“, erklärt Betriebsleiter Arnd Schneider. Spezialanfertigungen sind nur die Auflieger – Standardauflieger nach DIN würden nicht passen.
Bergmann Mario Christ gefällt sein neues Arbeitsgerät: „Der Econic besitzt die kompakten Maße eines Spezial-Bergbaugeräts, ist aber viel komfortabler. Das Allison 6-Gang-Automatikgetriebe schont die Nerven, die Luftfederung den Rücken.“ Dank kraftvollem Motor und robustem Retarder im Econic 1835 ist im ausgedehnten Wegenetz unter Tage selbst voll beladen Tempo 50 möglich. „Da schafft man jeden Tag schon ordentlich mehr weg als früher“, sagt Mario Christ. „Gut ein Viertel mehr Motorleistung bei gleichzeitig gesunkenen Schadstoffwerten im Vergleich zum Vorgängermodell sind nicht nur für uns Bergleute ein enormer Fortschritt.“
Quelle: Transport-Magazin 2/2016
Text: Christian Schmidt
Fotos: Alex Kraus